Для изготовления качественных металлических изделий сегодня используют специализированная оснастка. Речь идёт, в частности, о матрицах и пуансонах. Ими оснащают штампы, прессы и другие приспособления для достижения максимальной точности размеров деталей. Это важно для получения качественных изделий, которые имеют товарный вид.
Матрица представляет собой металлический короб без крышки, благодаря которому будущее изделие приобретает свою форму. Полости или углубления в ней точно соответствуют форме и размерам желаемого изделия. Есть простые (для какого-либо конкретного типа изделия) и комбинированные (для разнотипной продукции) матрицы. Простые более распространены, в частности, в строительной сфере – они часто используются для изготовления пустотелого кирпича, различных блоков и прочих изделий.
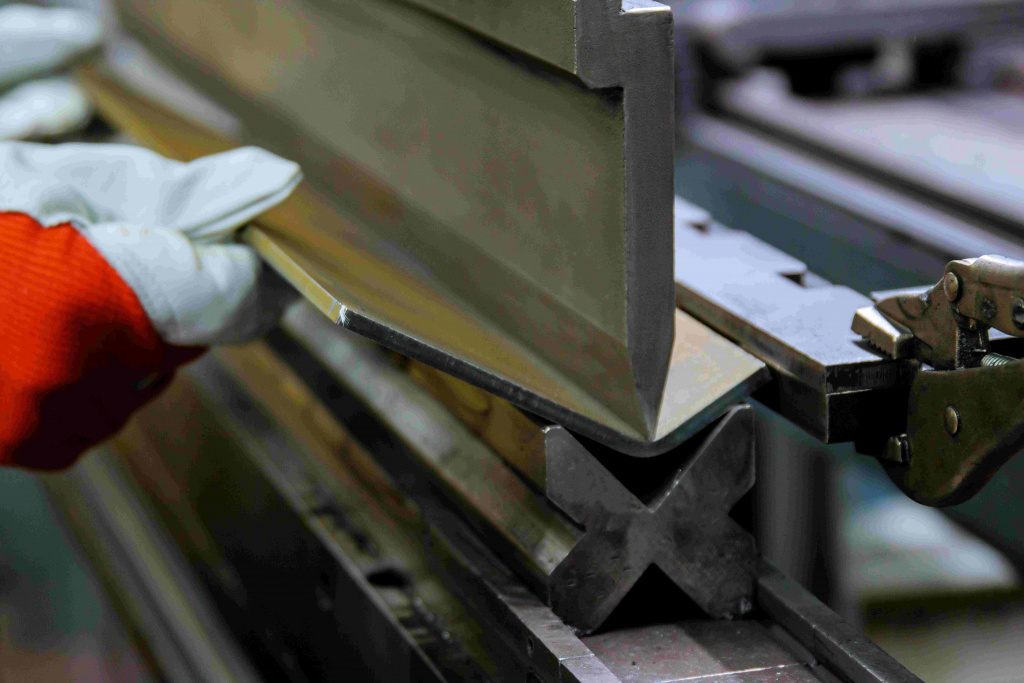
Пуансон, или пресс-штемпель – это, по сути, конструкция, формирующая верхнюю сторону будущего изделия. Она в точности совпадает с профилем матрицы, а по функциям сопоставима с прессом, маркировщиком или штампом. Другими словами – эта конструкция используется для выдавливания детали, нанесения на неё маркировки (можно в зеркальном, можно в обычном виде), а также для штамповки. С помощью пуансонов можно получить изделия сложных геометрических форм либо детали с большой степенью рельефности. Наиболее востребованы пуансоны в металлообрабатывающей и строительной сферах – и их помощью, в частности, выполняют гибку листового металла, прессование, а также изготовление разнотипных газобетонных и шлакоблоков.
Среди основных плюсов промышленного использования пуансонов можно назвать то, что они обеспечивают высокую точность и повторяемость изделий, позволяют создавать сложные детали, существенно сокращают время производства и удешевляют его стоимость, а также уменьшают количество материала, который необходимо обработать.
Виды пуансонов
Пуансоны бывают разные, отличаются они по нескольким основным критериям.
По типу конструкции и назначению они делятся на:
- прошивные;
- пробивные;
- вырубные;
- просечные.
Условия эксплуатации данных изделий весьма специфические – рабочий процесс проходит при высоком давлении, а часто ещё и при воздействии высоких температур. Поэтому для получения качественного изделия высокой точности, а также во избежание деформации самой конструкции, материалы, из которых изготовлен пуансон, должны отвечать ряду требований.
Материалы для изготовления пуансонов
Чтобы система работала максимально долго и не требовала замены, для её изготовления используются следующие материалы.
Сталь. Как материал, обладающий большой стойкостью к износу, отлично подходит для изготовления подобных конструкций. Для горячих рабочих процессов используются износоустойчивые стали с высокой прочностью при температурах деформирования. Для пуансонов, задействованных при холодных рабочих процессах, применяется высокопрочная сталь повышенной прокаливаемости (степень закалки должна быть от 54 до 65 HRC) и инструментальная сталь марки 6ХВ2С. Эти материалы также отличаются устойчивостью к коррозии.
ВАЖНО! Легированная сталь в этом случае не подойдёт, поскольку она становится чересчур хрупкой, если регулярно подвергать её воздействию температур.
Полиуретан. Ещё один популярный материал для изготовления пуансонов. Он отличается высоким качеством, повышенной прочностью и устойчивостью к износу. Кроме того, он эластичный и при этом достаточно твёрдый.
Правильно подобранный пуансон гарантирует качество и точность производства деталей. Помимо повышенных требований к прочности и долговечности материала, из которого он изготавливается, для ровного и точного формирования будущего изделия поверхность пуансона также должна быть максимально гладкой и чистой.
Зазор между матрицей и пуансоном
Одним из очень важных моментов, требующих тщательного контроля для получения качественного конечного продукта, является зазор между матрицей и пуансоном. Есть определённые правила, которым должна соответствовать эта величина. В идеале, учитывая толщину заготовки и особенности материала, зазор должен быть не меньше 0,5 мм и не больше 12 мм, или от 4 до 16% от общей толщины заготовки. Максимально допустимый зазор при производстве деталей – 30%, однако при этом обязательно необходимо использовать оснастку с наиболее острыми режущими зонами.
При недостаточном зазоре поверхность среза может расслаиваться и рваться, соответственно, будет с заусенцами и неровностями. В случае же, если зазор будет чрезмерно большим, то тонкий материал будет втягиваться и в итоге просто разорвётся. В результате края изделия будут затянуты, а также появятся заусенцы. Если заготовка будет толстой, то при большом зазоре кромки готового изделия могут быть закруглены.
Таким образом, правильно определённый и настроенный зазор между матрицей и пуансоном является залогом получения соответствующей техпроекту конечной продукции с идеально точными размерами.
Основные этапы изготовления пуансонов и матриц
Есть пять основных этапов:
Заготовка. На этой стадии выбирается материал, из которого будет производиться конструкция. При этом учитывается тип материала для штамповки, его толщина и сложность формы будущего изделия. Надёжными считаются матрицы и пуансоны, для изготовления которых использована инструментальная сталь 42CrMO. Для повышения эксплуатационных качеств такие изделия дополнительно проходят индукционную закалку. Также на этапе производится распиловка – заготовку вырезают из выбранного материала лазером либо с применением плазменной резки или других методов.
Черновая обработка. Здесь будущая матрица или пуансон приобретают примерную форму с помощью фрезерного станка с ЧПУ. Также в изделиях просверливают все необходимые отверстия.
Термообработка. Третий этап, на котором сначала производится закалка будущих конструкций путём нагревания до температуры, превышающей критическую точку, и последующего резкого охлаждения. Таким образом достигается требуемая стойкость к износу и твёрдость. После этого происходит отпуск матрицы и пуансона при более низких температурах для снятия внутреннего напряжения и повышения ударной вязкости.
Чистовая обработка. На этой стадии выполняется шлифование деталей до необходимой шероховатости поверхности. Если есть такая необходимость, то также выполняют доводку рабочих поверхностей матрицы и пуансона. Для этого применяется специнструмент и абразивные материалы.
Контроль качества. Последний этап, когда продукцию проверяют на соответствие указанным в чертежах размерам и формам. При необходимости иногда матрицы и пуансоны испытывают на штамповочном прессе.
Применение пуансонов
Пресс-формование с использованием матрицы и пуансона востребовано в различных отраслях промышленности. Их располагают в прессе, где впоследствии происходит деформация материала под давлением и так создаются высокоточные детали.
Пуансоны изготавливаются разных форм и размеров, поэтому можно использовать их для разных пресс-формовочных операций. К примеру, в автомобильной промышленности таким способом производятся кузовные детали – капоты, двери, бамперы. В аэрокосмической с помощью пуансона создаются лёгкие и при этом довольно прочные элементы самолётов и космических аппаратов.
Пуансоны и матрицы: основные особенности
Для продления сроков службы матриц и пуансонов, специалисты советуют регулярно проводить обслуживание прессов и станков. Особенно рекомендуется уделить внимание очистке рабочего пространства и оборудования по завершении работы. Самым простым и эффективным способом очистки является механический – с помощью ручного инструмента (щёток, скребков и т. д.). Однако более серьёзные загрязнения лучше удалять посредством установок высокого давления. Перед следующим запуском специалисты рекомендуют тщательно просушить устройство.
Однако стоит помнить, что каким бы ни было качественным обслуживание и чистка оборудования, матрицы и пуансоны относятся к быстроизнашивающимся расходникам, и всё равно их придётся менять довольно часто. В зависимости от условий эксплуатации и особенностей производства средний срок службы пуансона и матрицы составляет до 6 лет.
Для получения качественной конечной продукции на матрицах и пуансонах не допускается наличие каких-либо неровностей, трещин, сколов и прочих дефектов.