Старые и новые технологии
Сварочные швы значительно старше современной металлургической науки. Новые эффективные технологии стали доступны только с момента изобретения электрода в середине 19 столетия. Но соединение деталей было известно человеку задолго до нашей эры. В Древнеегипетских гробницах археологи нередко встречают ювелирные и бытовые изделия из драгметаллов с весьма искусно выполненным швом. А при раскопках Помпеи были найдены водопроводные трубы из свинца с паяным продольным соединением.
В течение двух столетий не только развивается теория, но и совершенствуются практические навыки сварщиков. Используются разнообразные методы — в зависимости от конкретных производственных задач, чертежа, технического оснащения, стандарту ГОСТ и квалификации специалиста. Классификация соединений может проводиться по нескольким параметрам.
Основная градация — по конкретному расположению деталей друг к другу:
- Стыковое — работа с деталями, расположенными в одной плоскости.
- Нахлесточное — элементы соединяются по принципу ступеней, образуя небольшой нахлёст.
- Угловое — заготовки свариваются перпендикулярно друг к другу или под заданным углом.
- Тавровое — детали свариваются в форме буквы Т, под прямым углом или небольшим наклоном.
- Торцевое — элементы прилегают друг к другу плоскостями.
Стыковой и угловой варианты — наиболее распространённые и наименее сложные. Стыковой чаще всего используется для работы с трубопроводами и с листовым металлом.
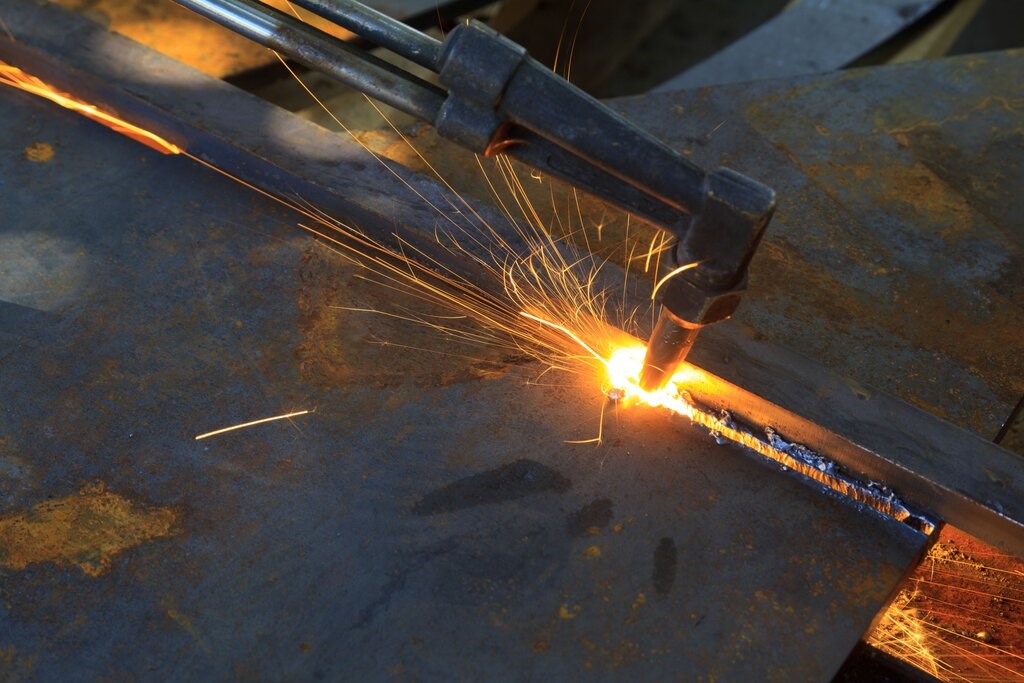
Немного терминологии
Новички нередко путают термины «сварочный шов» и «сварное соединение». Но это абсолютно разные технологические понятия. Сварочный шов — конкретный участок, соединяющий различные детали. Сварное соединение состоит из трёх элементов:
- Непосредственно место шва.
- Зона сплавления.
- Участок термического воздействия.
Сварка металлоконструкций включает самые разнообразные методы — с одними может справиться и начинающий рабочий, а для других требуется высокая квалификация. В некоторых случаях необходима без преувеличения виртуозная работа с электродом: его движение во время сварки может выполняться самыми различными рисунками:
- зигзаги;
- треугольники;
- спирали;
- полумесяцы;
- восьмёрки.
Если проводить электродом прямую линию, шов будет более тонким и ровным, но вот о долговечности такого изделия можно забыть. Создание электродом сварочного рисунка делает шов шире, но при этом обеспечивает его прочность и надёжность.
Типы сварных соединений
Шов, полученный в результате кристаллизации металла, должен быть неразъёмным и надёжным, герметичным и долговечным. А вот критериев, по которым определяется оптимальный вид шва, множество.
Наиболее простой — по пространственному положению свариваемых элементов:
- горизонтальный;
- вертикальный ;
- потолочный;
- нижний.
Самая сложная работа — с потолочным, верхним швом. В этом случае подтёк металла не только влияет на качество изделия, но и создает реальную угрозу для человека — ведь раскалённый металл находится прямо над головой сварщика.
Как при вертикальном (сварка электрической дугой), так и горизонтальном способе главный риск — подтекание и деформация металла. Здесь этот процесс не так опасен для человека, но губителен для качества работы. А вот нижний тип сварки прост, практически безопасен и доступен начинающему специалисту.
Следующий критерий — протяжённость шва. ВАЖНО: независимо от размера швы могут быть сплошными и прерывистыми. По протяжённости соответствуют трем группам:
- Длинный — свыше 1 метра.
- Средний — от 25 сантиметров до 1 метра.
- Короткий — менее 25 сантиметров.
Прерывистые представляют собой отрезки 0,1-0,3 метра, можно указывать несколько типов:
- шахматный;
- точечный;
- цепной.
По внешнему виду сварные швы также делятся на три категории:
- вогнутые — при работе с тонкими металлическими деталями;
- выпуклые — для более мощных конструкций;
- треугольные — как правило, применяется для угловых и тавровых соединений.
А вот плоский шов можно считать универсальным. Для него используется также определение «нормальный шов». Он прост в работе, надёжен в эксплуатации и способен выдержать внушительные нагрузки.
Разделяются виды сварочных швов и по самому виду сварки:
- Электродуговая ручная.
- Лазерная.
- Плазменная.
- С применением инертных газов.
- Автоматическая.
- Давлением.
Выбор конкретного вида зависит не только от условий работы, сочетания сварочных материалов, требований технологии — но и от квалификации сварщика, а также возможностей имеющегося оборудования.
Конфигурация — подразумеваются именно обозначение характеристики самого шва, а не свариваемых деталей:
- прямолинейный;
- криволинейный;
- кольцевой или скругленный.
Визуально кольцевой шов можно определить как спиралевидный.
По числу проходов — этот параметр зависит от толщины свариваемого металла и требований к прочности готовой конструкции. Таким образом, по числу проходов сварочные швы бывают:
- однослойные однопроходные;
- многослойные;
- многопроходные.
Вектор внешнего воздействия — подразумевается усилие, необходимое специалисту при сваривании деталей. Подразделяется на четыре варианта:
- Лобовой или поперечный — при векторе 90 градусов.
- Фланговый — означает усилие, параллельное стыку.
- Комбинированный — сочетает возможности других трёх вариантов и является самым сложным в выполнении.
- Косой — при направлении электрода под углом менее 90 градусов.
Существует ещё один простой вид классификации — шов может быть односторонним или двусторонним. А вот в зависимости от толщины деталей различной будет и подготовка сварочной кромки:
- детали толщиной менее 4 мм — с отбортовкой;
- до 8 мм — без скоса;
- 3-60 мм — V-скос;
- 8-100 мм — К-скос;
- 15-100 мм — криволинейный скос;
- 8-120 мм — Х-скос.
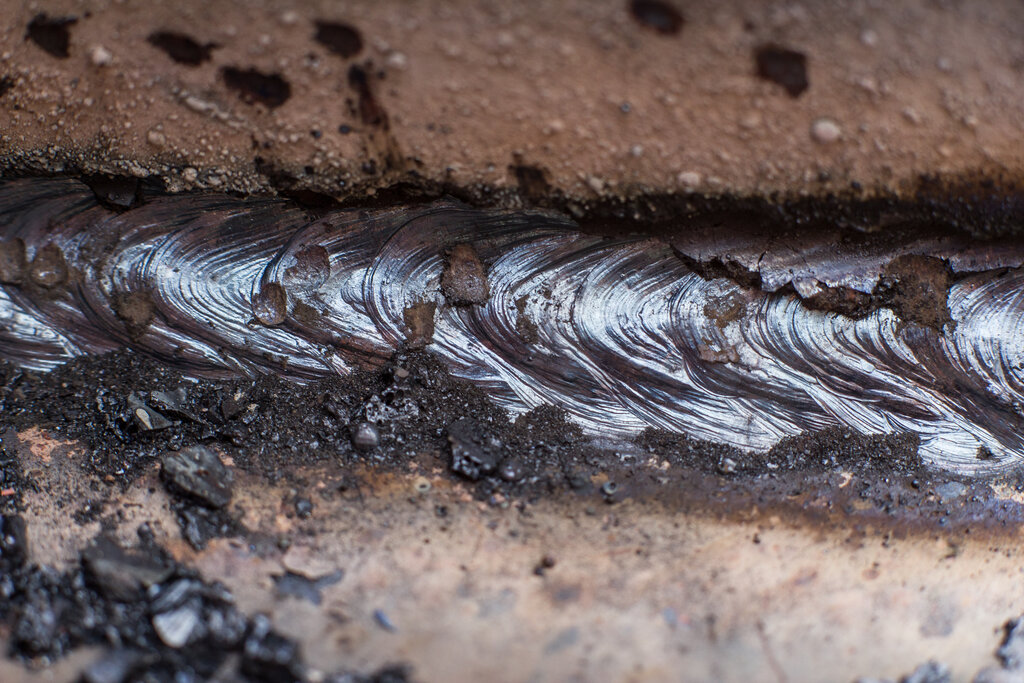
Работа с тонкими деталями, как правило, предусматривает стыковую сварку с односторонней обработкой либо без обработки конструктивного элемента кромок.
Какие существуют дефекты
Даже высокая квалификация и предельная внимательность рабочего не гарантируют безупречный результат. Проблемы могут образовываться не только из-за ошибок во время работы, пластической деформации металла, но и вследствие недостатков самого металла или сбоев в работе сварочного оборудования. Поэтому подготовка к сварке важна не меньше, чем сам процесс.
Какие проблемы наиболее часто встречаются:
- прожог;
- непровар;
- возникновение пор.
Ещё один возможный недостаток — шлаковые включения. К сожалению, в большинстве случаев дефекты становятся очевидны только по завершении работы. Одни проблемы можно устранить, выполнив повторную сварку, а другие приводят к выбраковке изделия.