Обработка отверстий — важнейшая технологическая операция в машиностроении и металлообработке. От её качества зависят прочность соединений, герметичность, работоспособность механизмов и внешний вид изделия. Разные методы обеспечивают разную точность и шероховатость поверхности, и выбор подходящей технологии требует глубокого понимания характеристик будущего отверстия.
Виды отверстий по форме и назначению
Наиболее распространённой формой является цилиндрическая — такая геометрия применяется в большинстве технических решений. Конические отверстия имеют сужение по длине и используются, например, для посадки конусных крепежей. Профильные отверстия отличаются нестандартной формой (например, квадратной, шлицевой, овальной) и часто выполняются в деталях с особыми требованиями к передаче вращающего момента или фиксации. Отверстия делятся также на сквозные (проходящие через всю деталь) и глухие (имеющие ограниченную глубину).
Функционально отверстия могут быть крепёжными (для болтов, винтов, шпилек), направляющими (для осей, валов, штифтов), технологическими (временными или вспомогательными), вентиляционными и маслопроводными. Назначение определяет точность и метод обработки: например, направляющие требуют более высокого уровня точности, чем технологические.
Основные методы обработки
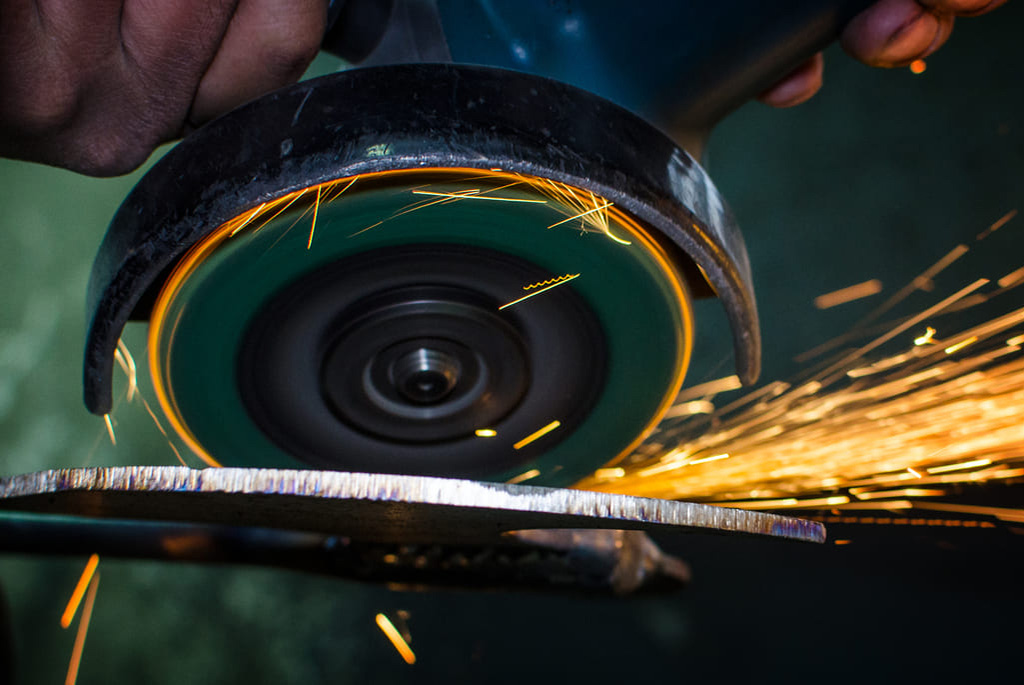
Благодаря современным технологиям обработки отверстий у специалистов в доступе широкий спектр операций — от грубой черновой обработки до высокоточной финишной доводки. Ниже рассмотрим ключевые методы.
Сверление
Это основной способ получения отверстий. Чаще всего используется спиральное сверло, которое позволяет формировать как сквозные, так и глухие отверстия в различных материалах. Однако точность сверления ограничена — как правило, отклонения составляют 0,1–0,3 мм. Шероховатость поверхности также относительно высокая, поэтому сверление обычно применяется как предварительный этап перед чистовой доработкой.
Зенкование и зенкерование
Зенкование применяется для формирования фасок и углублений под головки крепёжных элементов. Эта операция позволяет улучшить внешний вид соединения и повысить надёжность посадки. Зенкерование, в свою очередь, служит для точной обработки отверстия после сверления и позволяет устранить овальность, повысить точность по диаметру и снизить шероховатость.
Расточка
Расточка используется для точной обработки внутренних поверхностей отверстий с помощью одного или нескольких резцов. Этот метод подходит для отверстий большого диаметра или нестандартной формы. Расточка проводится на токарных, горизонтально-расточных и координатно-расточных станках. Точность может достигать 0,01 мм, а качество поверхности соответствует требованиям средней и высокой точности.
Развертывание
Развёртка — это многолезвийный инструмент, который применяют для окончательной обработки отверстий, особенно если требуется высокое качество посадки. Она снимает тонкий слой материала, обеспечивает точный диаметр и высокое качество поверхности — шероховатость может составлять до Ra 0,8 мкм, а точность — до 6–7 квалитета. Метод широко используется в машиностроении для посадок под валы и штифты.
Шлифование
Внутреннее шлифование применяется при необходимости достичь высокой точности и минимальной шероховатости поверхности. Используются абразивные круги малого диаметра, работающие внутри отверстия. Этот метод подходит для закалённых и твёрдых материалов, в том числе для окончательной обработки вала или втулки. Шероховатость поверхности может достигать Ra 0,2 мкм.
Хонингование
Хонингование — это финишная операция, обеспечивающая очень высокую точность геометрии и минимальную шероховатость. Инструмент с абразивными вставками совершает возвратно-вращательные движения, выравнивая микронеровности по всей длине отверстия. Метод особенно востребован при обработке цилиндров двигателей внутреннего сгорания и гидравлических компонентов.
Протягивание
Протягивание — это высокопроизводительная операция, при которой через отверстие протягивается специальный инструмент — протяжка, имеющая последовательно увеличивающиеся режущие зубья. Каждый зуб снимает тонкий слой материала, обеспечивая высокую точность и чистоту обработки. Метод идеально подходит для массового производства, а также для формирования шлицев, шпоночных канавок и отверстий сложной формы.
Какой метод обработки отверстий лучше выбрать
Выбор метода зависит от множества факторов: требуемой точности, материала заготовки, размеров отверстия, типа производства (единичное или массовое), а также от характеристик доступного оборудования. Для черновой обработки чаще всего применяют сверление. Если необходима повышенная точность, используются зенкерование, развертывание и расточка. При очень высоких требованиях к чистоте и геометрии поверхности применяют шлифование и хонингование.
Чтобы лучше ориентироваться при выборе метода, достаточно учитывать цель, с которой выполняется обработка:
Цель обработки |
Рекомендуемые методы |
Первичное получение отверстия |
Сверление |
Улучшение точности |
Зенкерование, развертывание, расточка |
Минимальная шероховатость |
Шлифование, хонингование |
Обработка сложных профилей |
Протягивание |
Массовое производство |
Протягивание, хонингование |
Почему важно обращаться к профессионалам
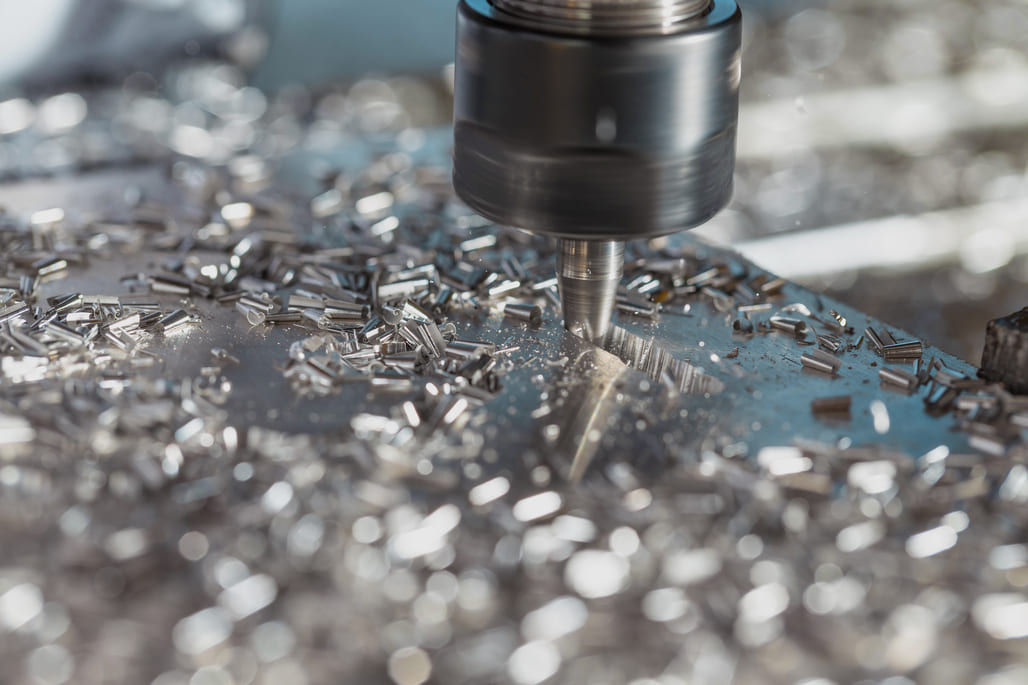
При обработке отверстий ключевую роль играют точность, расчёт режимов резания и знание свойств материалов. Ошибки при выборе инструмента, параметров подачи или скорости могут спровоцировать появление дефектов, брак или повреждение оборудования. Специалисты с опытом работы на станках с ЧПУ, расточных и шлифовальных станках способны:
- обеспечить соблюдение допусков и посадок;
- правильно подобрать режимы обработки;
- использовать качественный инструмент;
- выполнить работу в срок и с надлежащим качеством.
Кроме того, профессиональные цеха часто имеют в распоряжении более широкий спектр оборудования, включая специализированные развертки, хонинговальные головки, шлифовальные станки и измерительное оборудование.
Обработка отверстий — это многоступенчатый процесс, включающий черновые и чистовые операции. Он охватывает сверление, зенкерование, расточку, развертывание, шлифование, хонингование и протягивание. Каждый метод имеет своё предназначение и выбирается в зависимости от задачи. Чтобы добиться высокого качества и точности, особенно при массовом производстве или при работе с закалёнными сплавами, следует доверять выполнение работ квалифицированным специалистам. Это позволяет избежать брака, снизить производственные издержки и обеспечить надёжность готового изделия.
Для расчета развертки используйте наш калькулятор